스퍼터링이란?
일반적으로 스퍼터링이라고 불리는 스퍼터링 증착은 고체 타겟의 표면에서 원자/분자를 제거하여 다른 표면에서 응축되는 기체 상태로 투사합니다. 가장 간단한 배열에서는 두 개의 원형 평면 평행 디스크, 즉 몇 인치 간격으로 장착된 타겟(음극)과 기판(양극) 사이에 고전압이 적용됩니다. 1~100mTorr의 불활성 공정 가스가 전극 사이를 흐릅니다. 표적 표면의 초기 전자는 가스에서 계단식 이온화를 일으키고 전자와 양이온의 농도가 동일한 제한된 영역으로 느슨하게 정의된 플라즈마를 형성합니다.
플라즈마는 전기적으로 중성이며 전도성이 높기 때문에 전압 강하가 거의 없습니다. 드롭은 플라즈마와 각 전극 사이의 얇은 "암흑 공간" 영역에 걸쳐 발생합니다. 타겟의 음전위는 플라즈마 가장자리에서 양이온을 끌어당깁니다. 그들은 에너지 전달을 통해 중성 표적 원자/분자를 방출하기에 충분한 운동 에너지로 표적을 공격합니다.
표적에서 기판으로 이동하는 동안 방출된 각 원자는 수많은 가스 원자/분자와 충돌하여 방향을 바꾸고 에너지 손실을 유발합니다. 타겟-기판 거리를 최적화함으로써 원자는 부분적으로 무작위 방향에서 기판 표면에 접근하여 질감이 있는 기판 표면 전체에 합리적으로 균일한 필름 두께를 생성합니다.
원형 소스의 경우 타겟과 기판 사이의 최적 투사 거리는 소스의 링형 증착 패턴을 "부드럽게" 하기 위해 타겟의 직경보다 큽니다. 대조적으로, 가로질러 이동하는 넓은 면적의 기판을 코팅하는 데 사용되는 선형 생산 소스는 최적 투사 거리가 짧습니다. 여기서 선형 소스의 최종 효과는 균일성을 방해합니다.
스퍼터 소스
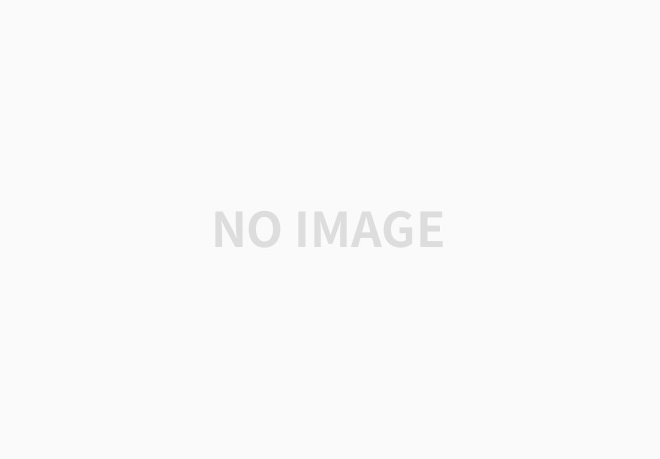
다양한 스퍼터 소스에 대한 다이오드, 마그네트론, 균형/불균형, RF/DC 전원 옵션 등의 차이점은 진공 시스템에서 논의됩니다.
소스의 진공 호환성은 특정 설계에 따라 다르지만 모두 10-6Torr ~ 10-7Torr 범위에 적합합니다. 일부 실제 UHV 버전은 10-10 Torr와 호환되며 400°C까지 베이킹 할 수 있습니다(공기 측에서 자석을 제거한 상태). 후자 그룹은 공정 가스로 다시 채우기 전에 공정 챔버가 UHV 조건(청결을 위해)에 도달해야 하는 경우에 사용됩니다.
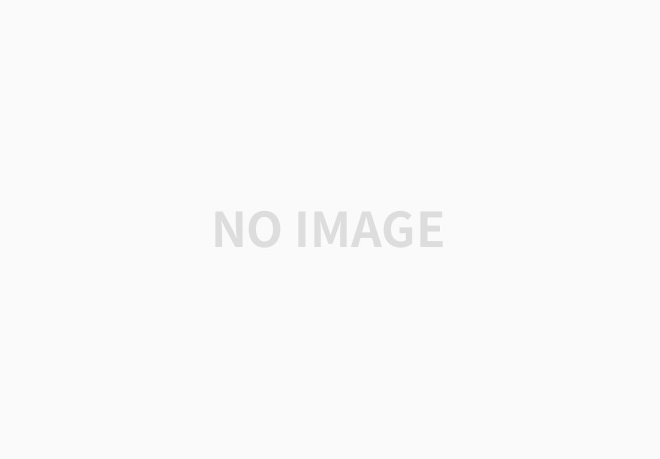
R&D 응용 분야에서 소스는 기존 챔버에 결합되는 경우가 많으며 소스 장착 포트와 기판 홀더의 상대적 위치에 따라 어떤 소스 장착이 가장 적합한지 결정됩니다. (i) 축 소스는 유틸리티 튜브에 수직인 대상 표면을 갖습니다. (ii) 직각은 유틸리티 튜브와 평행한 타겟 표면을 갖습니다. (iii) 플렉스에는 소스와 튜브가 플렉스 금속 호스로 연결되어 있어 중심선 사이의 각도를 0°에서 45°까지 변경할 수 있습니다.
R&D 응용 분야에 대한 추가 고려 사항은 필름 구성을 다양하게 하는 것입니다. 다양한 재료의 동시 또는 순차적 증착과 필름 구성의 빠른 변화를 위해 통합 교차 오염 차폐물, 셔터 및 가스 공급 장치가 있는 하나의 플랜지에 장착된 3개 또는 4개의 스퍼터 소스 클러스터가 이상적인 배열일 수 있습니다.
이는 더 두꺼운 타겟을 의미하며, 이는 해당 타겟을 관통하기 위해 올바른 모양의 자기장이 필요하다는 것을 의미합니다. 또 다른 일반적인 생산 요구 사항은 대형 직사각형 기판에 필름을 증착하는 것입니다. 이는 선형 스퍼터링 소스(기판 너비보다 길음)를 사용하여 해결된 다음 스퍼터링 중에 소스를 가로질러 기판을 이동합니다.
스퍼터 타겟
플라즈마에 들어가는 대부분의 전기 에너지는 타겟에서 열 에너지로 변환됩니다. 물은 소스를 통해 흐르고 직접 또는 간접 냉각을 통해 대상을 냉각합니다. 직접 냉각에서는 대상의 진공이 아닌 면에 물이 흐르게 됩니다. 분명히 타겟은 (a) 스퍼터 에칭이 진공 무결성을 손상시키지 않도록 충분히 두꺼워야 하며 (b) 물과 반응하지 않아야 합니다. 이러한 이유로 직접 냉각은 두껍고 반응하지 않는 타겟이 일반적인 대량 생산 소스에서 사용되는 경우가 많습니다. 간접 냉각의 경우 물은 소스 냉각 우물의 비진공 측(타겟이 고정되는 구리 '컵')을 냉각합니다. 간접 냉각은 소량 생산 및 R&D 스퍼터 소스에 사용됩니다. 간접 냉각 대상은 교체가 어렵기 때문에 냉각 우물에 접착되지 않습니다. 그러나 냉각정과 대상 사이의 열 접촉 불량은 심각한 문제의 원인입니다. 열전도율이 낮은 타겟(산화물, 질화물, 유리, 세라믹 등)이 스퍼터링될 때 특히 눈에 띄는 불량한 열 전달은 다음을 초래합니다. (a) 타겟의 열팽창 응력 균열; 또는 (b) 인듐 결합 타겟을 백킹 플레이트에 용융시키는 단계.
이러한 문제의 발생을 줄이기 위해 두 가지 접근 방식이 사용됩니다. (a) 열 전도성 폴리머 시트 또는 은 함침 페이스트를 타겟과 냉각 웰 사이에 배치합니다. (b) 일련의 느린 "램프 앤 소크"를 통해 전원이 공급되거나 차단됩니다. 실제로 이는 전력이 0에서 원하는 전체 스퍼터 전력의 20%까지 천천히 증가함을 의미합니다. 그런 다음 대상은 다른 램프가 시작되기 전에 몇 분 동안 해당 전력에 담가질 수 있습니다. 이러한 방식으로 출력을 높이거나 낮추는 것은 스퍼터링 및 증발 응용 분야 모두에 좋은 방법입니다.
타겟은 각각의 소스에 맞게 모양이 적절하며 원형, 선형, 원통형, 쐐기형, 레이스 트랙, 잘린 원추형 및 기타 다양한 형태가 사용됩니다.
![]() |
![]() |
![]() |
Indium Tin Oxide circular target | Tantalum linear target | Aluminum race-track target |
스퍼터링의 장점
- 증착되는 원자/분자의 운동 에너지는 일반적으로 몇 eV이므로 적절한 기판에 우수한 필름 접착력을 제공합니다.
- 스퍼터링에는 용융이 필요하지
- 재료가 기판에 덩어리를 '뱉어내는' 경우는 거의 없습니다.
- 소스는 어떤 방향으로도 장착될 수 있습니다.
- 플라즈마 전자는 "뜨거우나" 다른 종은 그렇지 않으며 기판으로의 복사열 전달이 거의 없습니다.
- 표면 적용 범위는 엄밀히 말하면 가시선이 아닙니다.
- 원소 혼합물, 합금 및 일부 화학 화합물은 화학양론의 변화 없이 스퍼터링될 수 있습니다.
- 반응성 스퍼터링(Ar에 O2 또는 N2 첨가)에는 다양한 응용 분야가 있습니다. 특히 열전도율이 낮은 타겟의 스퍼터링과 관련된 문제를 방지합니다.
- 선형 소스는 금속 및 무기 재료로 대면적 기판을 코팅합니다.
출처: Lesker
'진공 시스템' 카테고리의 다른 글
반도체 산업에서 사용되는 전기 기계 장치 및 진공의 중요성 (2) | 2024.12.08 |
---|---|
증발법 (Evaporation) (0) | 2023.10.18 |
TPD - 열 방출 측정을 통한 박막의 미세 구조 조사 (0) | 2023.10.18 |
UHV 표면 분석 애플리케이션을 위한 깊이 프로파일링 (0) | 2023.10.18 |
SIMS 적용분야 (2) | 2023.10.17 |